Adding fiber laser cutting to a fab shop despite limited budgets and space
BY BOB FARRELL
February 8, 2024 · in FAB Shop Magazine Direct
Driven by increased demands for precision, versatility and cost-effective production, a growing number of fabricators are considering the addition of fiber lasers to their cutting arsenal. These machines offer several advantages, including unparalleled accuracy, intricate cuts and minimal material waste. Their versatility supports the processing of plate and sheet in both ferrous and non-ferrous materials, such as carbon steel, stainless steel, aluminum, brass and copper. And, as fabricators prioritize automation and smart manufacturing, fiber lasers streamline production while enhancing overall operational efficiency.
While the thought of such technology may be tempting, there are issues that must be considered when adding any piece of equipment – not the least of these are cost and logistics. Investing in fiber laser cutting equipment often represents a substantial financial commitment. As such, it’s critical that the laser and its capabilities are fully maximized.
Similarly, fabrication equipment typically demands a substantial footprint on the shop floor. The need for adequate spacing is often driven by operational functionality, safety concerns, operational workflow and the potential for future scaling of production. Efficient space utilization becomes a delicate balancing act as every square foot of space becomes a valuable commodity.
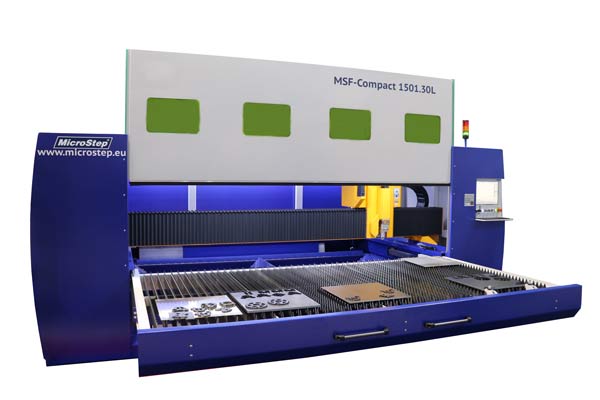
These factors can mean the difference between a healthy bottom line or a losing proposition. Consequently, decisions regarding machinery purchase, layout and arrangement create a serious dilemma for fabricators thinking about adding fiber laser cutting capabilities.
An easy decision
While removing equipment or adding floorspace might not be realistic, a practical alternative is to invest in equipment that occupies less space. John Prevish, national sales manager for United Precision Services, which represents a variety of machine builders, explains that the need for a compact solution is nothing new for the industry.
“When lasers were beginning to become mainstream in the marketplace in the early 1990s, small footprint machines were very common,” he says. “At that time, the commonly used CO2 laser system required a beam delivery system utilizing several mirrors to direct the laser beam from the power source to the cutting head. Properly aligning and maintaining these mirrors was complex, but more easily done on shorter length machines.
“Today, with the now-popular fiber laser, a fiber optic cable directs the laser beam to the cutting head instead of mirrors,” he adds. “By eliminating the use of mirrors, longer and wider laser cutting machines became commonplace in the industry.”
The industry, however, is rediscovering the benefits of a smaller footprint machine, which includes less required floor space, lower initial investment cost, the ability to do prototype work, and, simply, an option for those that don’t have high production needs or just prefer to outsource some of their laser work to maintain relationships with other shops.
For smaller manufacturers that see the benefits of a smaller footprint machine, MicroStep offers fiber laser cutting capability at a comfortable price point. With a variety of options, MicroStep’s MSF line is putting laser cutting into the hands of fabricators of all types and sizes. Per Prevish, the company has offerings ranging from 40 in. by 78 in. to 20 ft. by 164 ft.
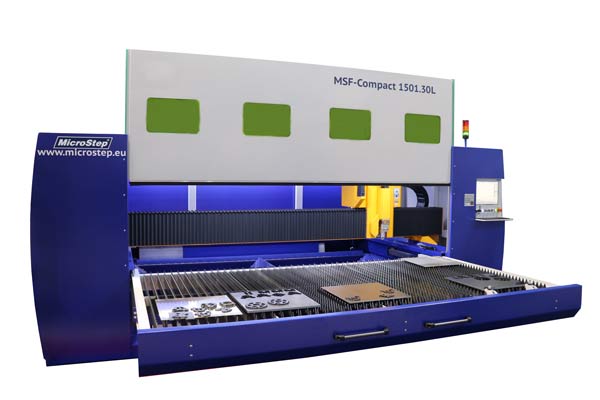
In terms of the company’s smaller footprint options, its MSF Compact serves as an ideal option for manufacturers looking for basic fiber laser cutting capabilities with limited floorspace. The machines are available in three sizes: 40 in. by 78 in.,4 ft. by 8 ft. and 5 ft. by 10 ft. Despite its small stature, the machine produces high-quality 2-D cutting at high speeds. A manually extractable cutting table enables easy and straightforward loading.
In terms of power, the compact model can still pack a punch with its maximum laser source power of 8 kW and maximum positioning speed of 7,204 ipm. The laser is equipped with a fully telescopic single grate system mounted on linear guidelines, which is pulled from the cabin to the front of the machine to ensure convenient loading and unloading.
The complete line
The MicroStep MSF line of fiber laser cutting equipment is available in a range of sizes, with various features and in multiple configurations. The product line includes:
MSF Pro: Powerful and versatile, this dual-pallet laser cutting system is available with cutting in 2-D (straight) or 3-D (bevel) in flat sheet and plate. This machine can be equipped with single or dual heads. In addition, pipe cutting from 1.18 in. to 20 in. in diameter can be added as well as drilling and tapping capabilities. Table sizes range from 5 ft. to 10 ft. wide and up to 40 ft. long.
For those requiring an even higher-performance machine, the MSF Pro X is available with a lightweight carbon fiber gantry that translates to faster gantry speeds, higher acceleration rates and higher jerk rates that result in more parts per hour. The lighter weight carbon gantry also provides improved stiffness and vibration dampening, resulting in less stress on machine components and increased performance and durability.
MSF Max: This giant among MicroStep’s fiber laser cutting solutions is available in a single table sized up to 20 ft. wide by 164 ft. long. This high-speed cutting machine comes standard with 2-D cutting, but can also be quipped for 3-D cutting as well as drilling and tapping capabilities.
For those that require more access to the cutting table, the MSF Max comes in a “C” version with a compact safety cabin that encapsulates just the gantry instead of the whole work area. The Max C has the same features as the MSF Max, but requires significantly less installation space. It’s ideal for customers that still need to cut long parts but have limited floorspace.
MSF Cut: This is a traditional high-performance 2-D laser cutting machine available in table sizes of 5 ft. by 10 ft., 6.5 ft. by 13 ft. and 6.5 ft. by 20 ft.
MSF Flex Plus: This is a traditional 2-D laser cutting machine for those that value low-cost versus high-performance without compromising on quality. It is available in table sizes of 5 ft. by 10 ft., 6.5 ft. by 13 ft., 6.5 ft. by 20 ft. and 8 ft. by 20 ft.
MSF Pipe-T: This laser pipe cutting machine with manual loading of pipes is designed for 2-D or 3-D cutting of round pipes up to 20 in. in diameter as well as for rectangular tubes and other cross-sections up to 11 in.
MSF Pipe AT: This higher level automated laser pipe cutting machine is ideal for round and square pipe up to 8 in.
Putting it to work
In Germany, the focus of TransPofix, a metals fabricator for the automotive, commercial vehicle and aerospace industries, is on the development, design and prototyping of tools for injection molded parts. For many years, laser cutting of these parts was outsourced. With a lack of prototyping flexibility and increased demand, the company set its sights on bringing fiber laser cutting in-house.
“If you’re not innovative, you slowly lose the market,” says Maciej Mackowiak, project manager at TransPofix, about the constant need for modernization. “Our strengths are flexibility, fast response times and short decision-making processes.”
Development times are getting shorter, and the market requires an even faster reaction to technological developments. Consequently, outsourcing was also a problem in prototyping.
“Delivery times were often very long,” Mackowiak says. “We also had a problem if something changed during the production of the prototypes. That meant order again, wait again.”
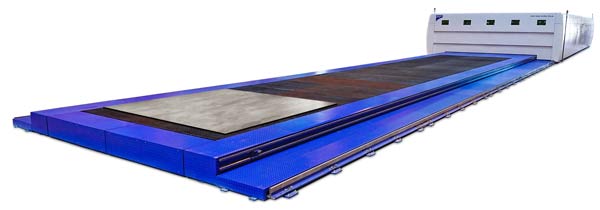
It was obvious, therefore, that the company needed the capacity to bring cutting in-house to react quickly and provide some independence from subcontractors. In short order, the company began evaluating cutting solutions and based on the materials that needed to be cut, quickly discovered that fiber laser technology offered the best solution. After a few test cuts, MicroStep’s MSF Compact was selected and has been in operation since January 2020. At first, it was primarily used for prototyping purposes but later, was also used for serial production.
“We made the decision in favor of the laser system because of the speed and the quality,” Mackowiak says. “In many cases, we can install the freshly cut part straight away without any rework.”
Maximizing investment
The fabrication floor is the hub of production and heart of the business. It’s where money is made or lost. Consequently, real estate is at a premium and the purchase of equipment and allocation of space are critical considerations.
Manufacturers must balance what they need with what they can afford and accommodate. With its MSF Compact, MicroStep offers a practical solution for fabricators that see a business case for adding fiber laser cutting despite space limitations. And with their expertise, the team at United Precision Services can answer any questions that fabricators might have to help them determine what is the best choice for their business.