Selecting an advanced fiber laser cutting machine represents a major investment for any manufacturing operation. The right fiber laser system can significantly boost productivity, efficiency, quality, and capabilities. As experts in large-format CNC solutions, United Precision Services helps manufacturers navigate the process to find their perfect fiber laser cutting system.
When weighing your options, it’s essential to fully understand the machine’s capabilities and advantages compared to alternatives. You must also realistically assess your materials, workload requirements, operating environment, and growth plans when selecting a fiber laser cutter.
This guide provides an in-depth look at what to consider when investing in a fiber laser cutting machine, so you can choose the optimal system to meet your manufacturing needs.
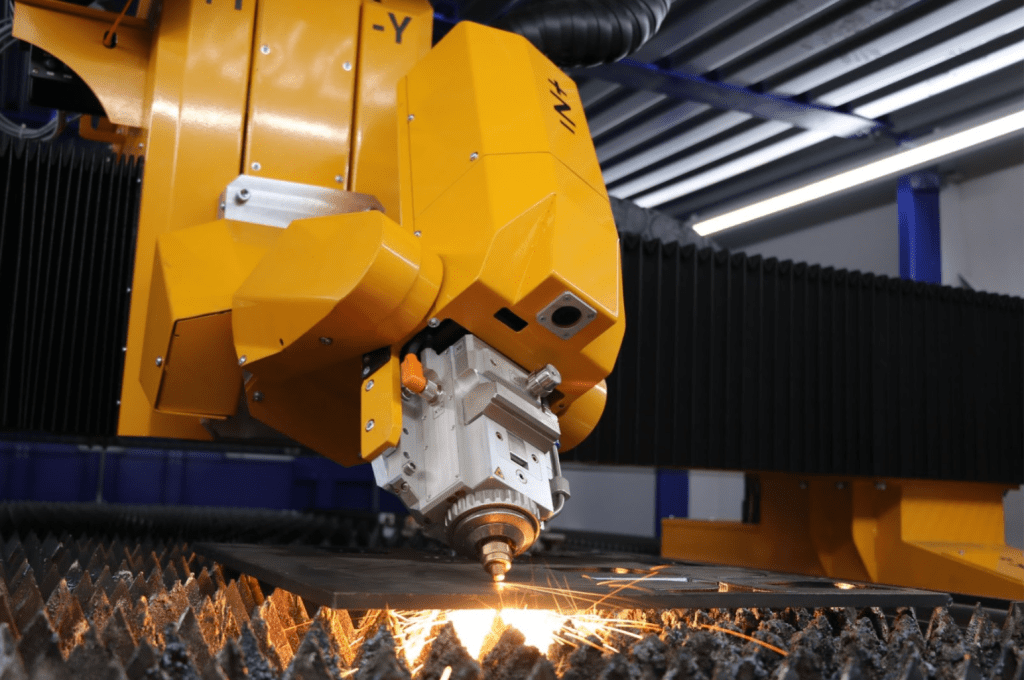
An Introduction to Fiber Laser Cutting Machines
Fiber laser cutting machines employ a high-powered laser to make extremely accurate cuts through metal, from thin aluminum to thick steel. The fiber laser’s intense beam melts through the metal, propelled by oxygen or nitrogen assisting gas to blow away molten material.
This advanced automated process makes clean, fast, precision cuts and holes unattainable by manual methods. It’s vastly more efficient than mechanical cutting tools. Fiber lasers in particular can handle highly reflective materials like aluminum that CO2 lasers struggle with.
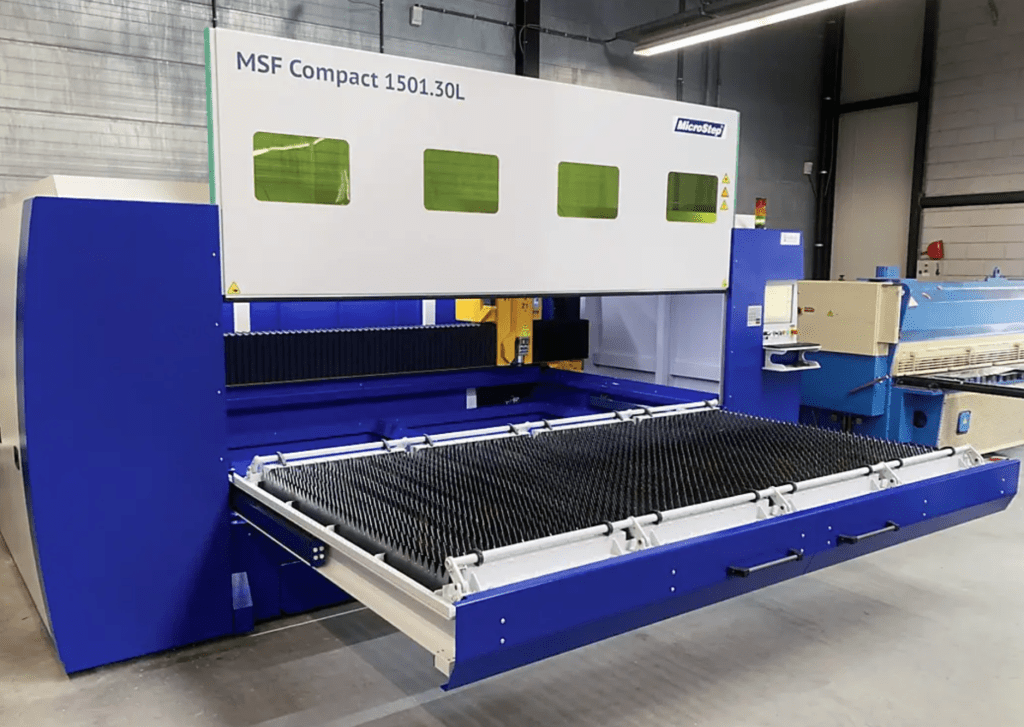
What Are Fiber Laser Cutters?
Fiber laser cutting machines are CNC machines that direct an industrial laser to slice through metal. They’re called “fiber” lasers because they generate laser light via an optical fiber that contains rare elements like erbium or neodymium, rather than the fragile glass tube setups of CO2 lasers.
Fiber laser machines offer key advantages like stable beam quality, smaller beam size, and greater efficiency that translate to faster, cleaner cuts. Their solid-state construction also makes fiber laser metal cutting machines more reliable and easy to maintain.
How Fiber Laser Machines Work
Inside fiber laser metal cutters, laser light at infrared wavelengths travels from the resonator through the routing fiber optics to the cutting head. Focusing lenses concentrate the beam’s power on a tiny spot on the workpiece.
Oxygen, nitrogen, or, more rarely, compressed air then propels the melted and vaporized material out of the kerf (cut). The cutting head assembly moves along the X and Y axes following CNC-programmed toolpaths while the metal stock remains stationary.
Industrial fiber lasers can modulate power from 1kW to 30kW watts for flexibility in materials and applications. Higher power equals faster cuts and thicker section capability.
Fiber Laser Machines vs. CO2 Lasers
CO2 laser cutters use focused beams of infrared light generated by manipulating electricity through mixtures of carbon dioxide, nitrogen, and helium gas. These gas mixtures flow through evacuated glass tubes flanked by mirrors that direct the laser toward cutting heads focused on the workpiece.
CO2 lasers ruled earlier generations of laser cutting machines but have some limitations compared to superior fiber laser technology:
- Fiber lasers cut faster than CO2 lasers thanks to more concentrated beam power. Feed rates are 2-3 times quicker.
- Fiber lasers produce higher quality cuts with narrower kerf, smoother cut surface finish, and smaller heat affected zones.
- Fiber lasers reliably and efficiently cut highly reflective metals like aluminum, brass and copper that CO2 lasers struggle with.
- Fiber lasers are more energy efficient.
- Fiber laser resonators have no moving parts or mirrors requiring alignment like high-maintenance CO2 lasers.
If your application involves mostly stainless steel or mild steel, a CO2 laser remains a viable lower-cost option. But for aluminum and mixed-metal fabrication, a fiber laser cutting machine is the clear choice.
Factors to Consider When Choosing a Fiber Laser Machine
Purchasing any large CNC system like a fiber laser cutting machine presents a major business investment. Choosing wrong can lead to productivity headaches and financial waste.
Thoroughly assessing these key considerations will help you make the right decision:
The Materials You Need to Cut
Think carefully about which metals you currently — or plan to — cut within your manufacturing operations. Document the metal types, thicknesses, diameters, or dimensions you expect to process on the fiber laser cutting machine over its service lifetime.
Provide this cut material information to reputable fiber laser manufacturers so their engineering team can specify adequate machine power, cutting speed, and motion system capacities to reliably handle your work. Trying to save money with an undersized machine inevitably backfires through lost contracts and weak cut quality issues.
Machine Power and Cutting Speed
The power rating of a fiber laser machine’s beam directly determines how fast it cuts and how thick it cuts. For example, 4kW can cut up to ¾ inch inch mild steel, while 8kW can cut up to 1-inch thick stainless steel.
Maximize your production pace by selecting a laser cutter with adequate power to efficiently cut your metal at fast speeds. This will allow your company to achieve fast laser engraving speeds without overbuying needless wattage that adds costs. Factor in some 20-30% extra power for increased workload flexibility. Then, ensure the motion system can dynamically accelerate and control at velocities aligned with the available laser power.
Ease of Use and Automation
Seeking out fiber laser cutting equipment with intuitive controls and programming reduces training time and boosts productivity. Many machines feature touchscreen interfaces, assisted setup wizards for novices, and offline programming modules to simplify creating cut patterns.
Automating the cutting process via CNC further frees operators for higher-value handling tasks while preventing fatigue issues, which are common with manual cutting equipment. Further probe automation features like automated lens and nozzle cleaning, focus control, and material handling to minimize production delays.
Durability and Maintenance
Like any machine tool investment, fiber laser cutters must withstand heavy daily use over the years. Review testing validation reports and customer case studies on prospective brands to study longevity in real-world environments and operations similar to your company’s.
Investigate your potential laser machine provider’s capabilities for localized service support to diagnose problems quickly and supply spare parts. The availability of cost-efficient spare parts stocked regionally prevents slow overseas shipments from stalling production during equipment issues.
Choose reputable brands like United Precision Services representing globally proven CNC builders to receive the best in responsive lifetime support.
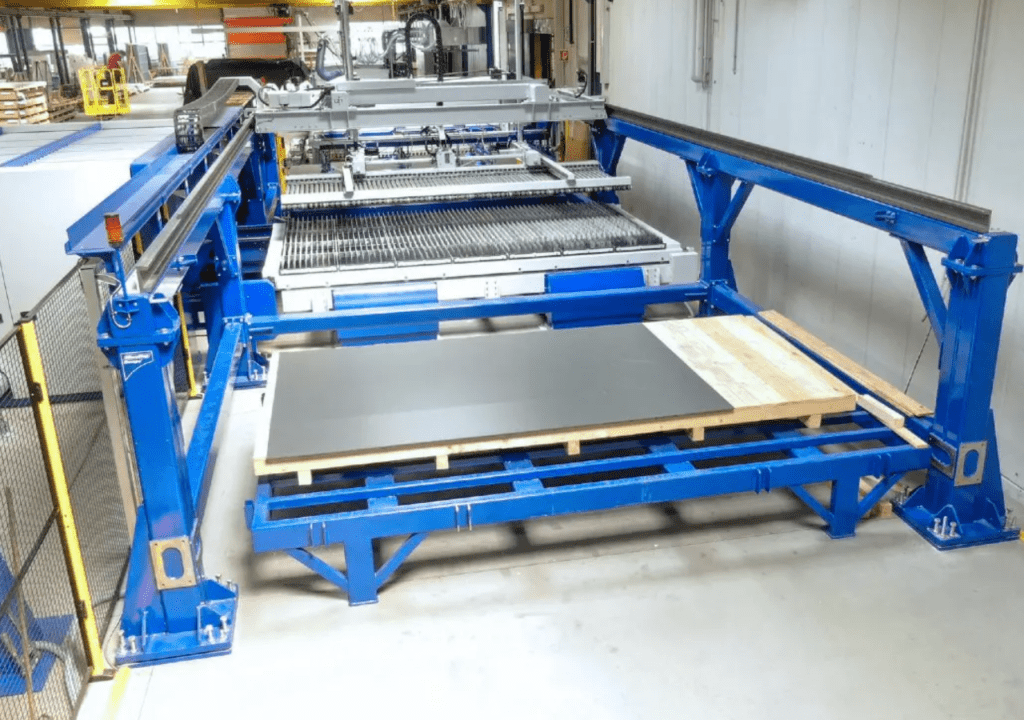
Training and Operational Safety for Fiber Laser Cutting Machines
Mistakes made operating powerful equipment like fiber laser cutting machines risk injury, scrapped materials, and damaged equipment. Comprehensive training in standard safety protocols, hazard awareness, and proper operating techniques helps ensure the well-being of staff, peak production uptime, and first-time quality cutting.
Basic Training Requirements
All personnel working around an industrial fiber laser machines should complete baseline safety and operational training before the machine’s live commissioning, detailing:
- Correct equipment guarding mechanisms
- Emergency stop procedures
- Precise movements within the safety zones
- Correct assisting gas hookups
- What and what not to cut
- Fire hazards and mitigations
- Workspace tidiness discipline
- Importance of personal protective equipment (PPE)
Safety Measures When Using Fiber Laser Cutting Machines
Employees should follow these rules when operating fiber laser cutting machines for the safety of themselves and others:
- Fully enclose the machine, use edge masking, and install fume extraction.
- Ensure reliable beam containment measures prevent laser light from escaping.
- Allow only qualified technicians into the laser generator enclosure.
- Confirm spill trays catch leaks from coolant and hydraulic systems.
Additionally, they must adhere to safe practices during cutting work:
- Wear appropriate laser safety goggles matched to the beam wavelength.
- Don protective apron, gloves, closed shoes, and ear plugs near operating machines.
- Keep the area around machines clean and free of slip, fall, and fire hazards.
Why CNC Laser Cutters Are Safer
Damaged equipment or materials can deal a huge blow to productivity and profitability. That’s why we always emphasize comprehensive operator training as well as purpose-engineered safety features when supplying fiber laser cutters optimized for your environment. Upgrading to automated CNC-controlled fiber laser cutting systems enhances safety in several key ways:
- Removing direct manual adjustment needs during live cutting.
- Enabling complete workspace enclosure without impacting function.
- Standardizing procedures programmed offline to prevent procedural mistakes.
- Ability to run unattended continuously outside normal working hours without risk of fatigue issues.
- Detecting problems automatically to halt cutting instead of limping through manual mode.
Properly integrated CNC engineering also tracks tool life and performance for preventative services that detect potential hazards ahead of actual failure. By engineering out the variability and fatigue risks inherent with manually operated equipment, CNC fiber lasers promote safer and more consistent production. As your manufacturing solutions partner, United Precision Services will ensure safety is designed into your customized fiber laser system.
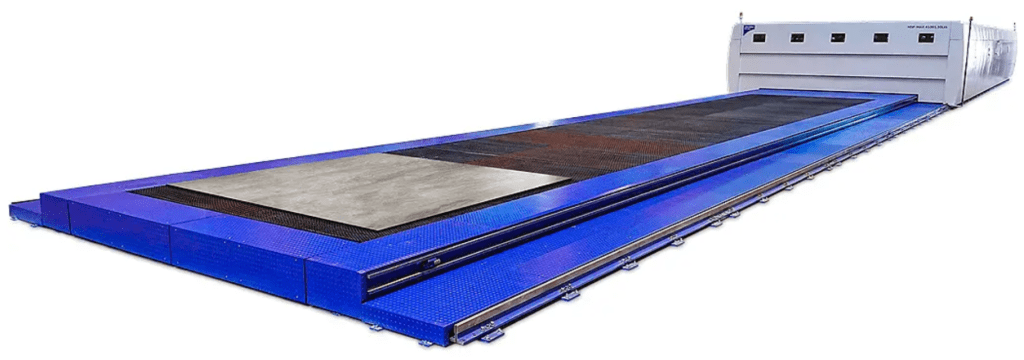
Choose Powerful Laser Cutting Systems from United Precision Services
With over two decades of experience supplying heavy-duty CNC solutions to leading manufacturers, United Precision Services understands the importance of speed, precision, and engineering detail in laser cutting machines. We are dedicated to matching customers with fiber laser metal cutters and other CNC systems that meet their exact production requirements.
Combining globally proven machine builders with localized service and support, we sell, install, and train your teams on premier fiber laser cutting technology applied in industries from aerospace and energy to transportation and mining.
Trust United Precision Services to deliver a custom-tailored fiber laser cutting machine solution for your production environment.
FAQs
What materials can a fiber laser cut?
Fiber lasers are highly versatile and efficient tools capable of cutting a wide range of materials. They are particularly effective for cutting metals, including carbon steel, stainless steel, aluminum, brass, and copper, offering precision cuts even for complex designs. Additionally, they can handle various thicknesses with ease, making them suitable for different industrial applications.
What industries use fiber laser cutting machines?
Key applications include contract manufacturing, metal fabrication, aerospace, automotive, appliance manufacturing, HVAC, electronics, construction, transportation, energy, medical devices, and more.
What safety precautions are necessary when using a CNC laser machine?
When using a CNC laser machine, it is crucial to adhere to specific safety precautions to avoid accidents and injuries. Always wear appropriate protective eyewear to shield your eyes from harmful laser radiation. Additionally, ensure the workspace is well-ventilated to avoid the inhalation of dangerous fumes that may be emitted from materials being cut or engraved. Operating the machine in accordance with the manufacturer’s instructions and undergoing proper training on its use are also vital steps for safe operation.
Which is better, CO2 or fiber laser?
Deciding between a CO2 and a fiber laser depends on the material and application in question. CO2 lasers are better suited for cutting, engraving, and marking a wide variety of materials, including plastic, wood, glass, and paper, making them highly versatile for different industries. Fiber lasers, on the other hand, excel at processing metals and are known for their efficiency, precision, and lower maintenance requirements, making them ideal for metal marking, etching, and cutting applications.