The oxyfuel cutting process utilizes a combination of compressed oxygen and fuel gases to slice through metal. This thermal cutting method has been relied upon for over a century thanks to its precision, versatility, and cost-effectiveness.
As leaders in premium large-format thermal machinery, United Precision Services offers top-tier CNC machine brands for manufacturers that require this fundamental yet advanced fabrication technique. Read on to learn the basics behind oxyfuel cutting.
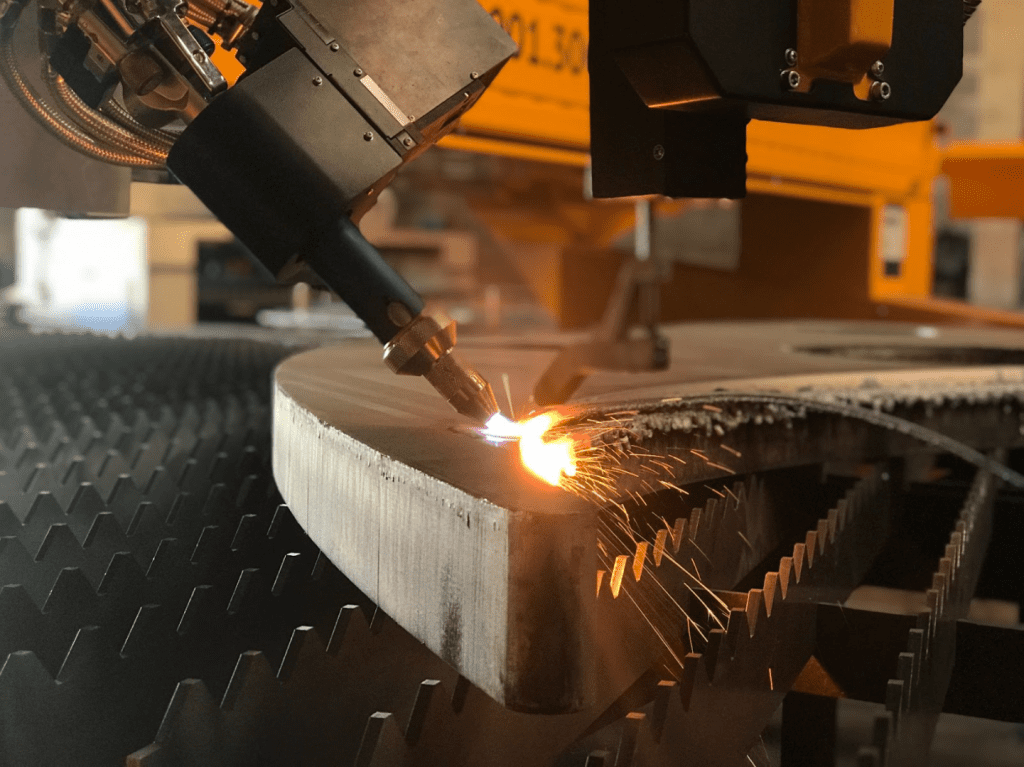
The Basics of Oxyfuel Cutting
What Is Oxyfuel Cutting?
Oxyfuel cutting, also known as oxyfuel flame cutting, is an essential process for cutting mild steel and low alloy steel. It involves focused heat from a flame produced by ignited compressed oxygen and fuel gas.
This flame heats the metal to its kindling temperature so that a stream of pure oxygen can then oxidize the metal and blow away the resulting slag. The torch tip continues moving along the metal to maintain the cut.
Material Preparation
Prior to oxyfuel cutting, the surface of the mild steel workpiece must be prepared by removing coatings, oils, and scales that could contaminate the cut quality or hinder the ignition of the cut line. This involves thoroughly cleaning the stock with degreasers, solvents, or abrasives.
Wire brushing, grinding, sanding, or blasting removes adherent scale layers, facilitating better heat absorption. The material is also typically marked along the intended cutting path on the surface. Quality material preparation results in faster, truer oxyfuel cuts.
When Should the Oxyfuel Cutting Process Be Used?
This process is ideal for cutting mild steel over 2 inches thick. It can produce clean, smooth cuts in materials up to 12 inches thick. While slower than plasma cutting on thinner materials, oxyfuel remains unmatched for cutting heavy steel plates up to 35 inches thick. It also allows versatile edge preparations like beveled cuts.
Industries like structural steel fabrication, machine shops, public works, shipbuilding, construction equipment, military vehicles, and more can benefit from oxyfuel’s heavy plate cutting capacities.
The oxyfuel cutting process is particularly suited to manufacturers producing large mild steel components, weldments, or custom plate work. Its precision and versatility across medium to thick stock make it a mainstay technology for metal fabrication.
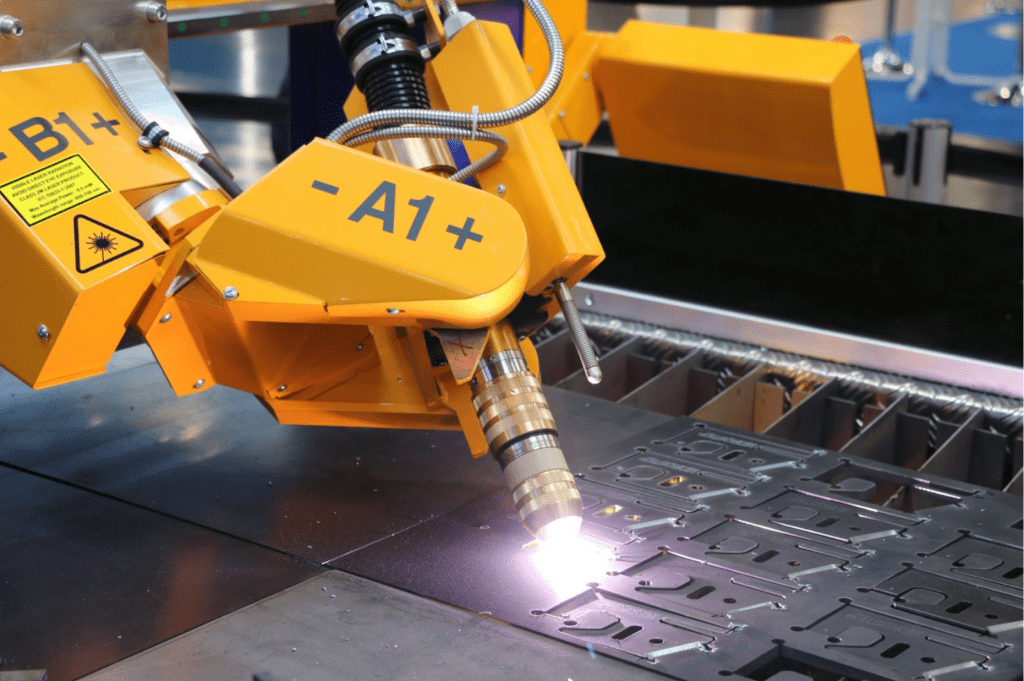
Oxyfuel flame cutting relies on an apparatus that supplies and controls oxygen and fuel gas flow to the torch. Cutting machines range from manual torches to computer-controlled machinery able to manipulate multi-torch arrangements.
Different Categories of Oxyfuel Cutting Machines
There are two main categories of oxyfuel machines – straight cutting and bevel cutting:
- Straight cutting oxyfuel machines make perpendicular cuts through a mild steel plate. They allow hole piercing and quality straight cuts without secondary processing.
- Bevel cutting oxyfuel machines produce angled cuts to prepare plate edges for welding. Common bevel cut types include V, Y, X, and K shapes in a range of angles.
Both varieties come in manual and automatic CNC formats to drive single or multiple cutting torches.
Straight cutting machines cut faster, but beveling machines enable more applications.
Factors That Influence the Quality of Oxyfuel Cuts
Achieving optimal oxyfuel cut quality requires careful control over operational parameters. The characteristics of the base material, torch setup, gas delivery system, and manual technique or automated programming all impact the resulting cut edge and throughput efficiency. Here are the key criteria that have the largest impacts on cut accuracy, surface finish, and speed:
- Material Type and Thickness: Oxyfuel performs best on mild steel. Attempting stainless steel cuts requires special methods, and materials under 2 inches risk warping. Ideal thicknesses range from 2 inches to 12 inches, but oxyfuel can cut up to 35-inch steel plates.
- Gas Flow and Pressure: Higher oxygen purity (99.5%+) enhances cut speed and quality. Uniform gas pressure prevents velocity changes that disrupt the cut. The choice of fuel gas, such as propane, natural gas, or acetylene, also impacts performance.
- Cutting Speed and Cutting Angle: Moving the torch at an appropriate speed along the planned cut path ensures an even, high-quality result. Automated systems excel at maintaining optimized torch travel rates for consistent quality. The angle of the torch to the workpiece further influences the cut and finished edge.
Advantages and Disadvantages of Oxyfuel Cutting
Oxyfuel cutting presents users with an array of unique benefits alongside some notable limitations. Evaluating this balanced profile allows manufacturers to appropriately match the process to suitable applications to leverage its capabilities.
Benefits of Oxyfuel Cutting
Oxyfuel flame cutting delivers numerous performance and economic benefits that make it an essential thermal cutting process, including:
- Produces exceedingly precise, clean-cut edges without secondary finishing required
- Achieves remarkable cut accuracy and surface perfection
- Well-suited for strict tolerance fabrication
- Handles the widest range of material thicknesses up to 35 inches
- Stays productive and cost-effective through heavy 12-inch sections
- Versatility supports small-scale prototyping to large custom work
- Most affordable entry point into metal cutting
- Modest equipment investment for manual rigs
- Compact footprint
- Reliable and easy to repair
- No complex programming skills necessary
Drawbacks of Oxyfuel Cutting
Like any process, oxyfuel cutting has some inherent limitations:
- Limited material compatibility beyond mild and low alloy steels
- Struggles maintaining precision below 2 inches as heat can distort thin stock
- Peak pierce capacity around 35 inches restricts practical limits without pre-drilling
- Pressurized gas fuels and oxygen necessitate extensive safety precautions
- Operational risk factors limit applications for some facilities
However, oxyfuel remains an efficient, clean, and versatile cutting technique for medium to thick mild steel. Trust United Precision Services to maximize its precision and value through premium equipment and support.
Choose Durable Oxyfuel Cutting Machines from United Precision Services
United Precision Services provides premium oxyfuel thermal cutting machines designed for heavy-duty, large-part manufacturing. As the leader in large format CNC solutions, we offer durable oxyfuel rigs precision-engineered to maximize cutting efficiency.
Our collection of industry-leading international brands delivers technologically advanced oxyfuel equipment with the power and versatility to meet your plate processing requirements. We help optimize torch arrangements and machine capabilities to fit your operational needs for material type, dimensions, edge preparations, and production volumes.
As specialists with decades of expertise, United Precision Services gives you a competitive edge via value-added services spanning your oxyfuel technology. This includes installation, training, servicing and support, rebuilds, part programming, fixture and foundation design, and more.
FAQs
What Materials Can You Cut with Oxyfuel?
Oxyfuel cutting works on mild steel and low alloy steels. It generally doesn’t cut stainless steel without special methods.
What Thickness of Steel Can Oxyfuel Cut?
Oxyfuel cuts mild steel from 1/8 inch to 35 inches thick. The typical ideal thickness range is 2 inches to 12 inches.
What are the Pros and Cons of Oxyfuel Cutting?
Oxyfuel cutting offers several advantages, including its ability to cut through thick sections of mild steel at a relatively faster rate and with minimal preparation time. However, the cons include a limited ability to cut non-ferrous materials such as aluminum and stainless steel effectively.
How do I Choose an Oxyfuel Cutting Machine?
Key factors to consider when selecting a machine are the types of cuts needed, the level of automation preferred, the number of torches required, the material thicknesses/types to cut, production volumes, and budget.